一種鋁型材擠壓模具鋼的熱處理工藝的制作方法
2023-05-20 09:38:01
來源:admin
閱讀量:0
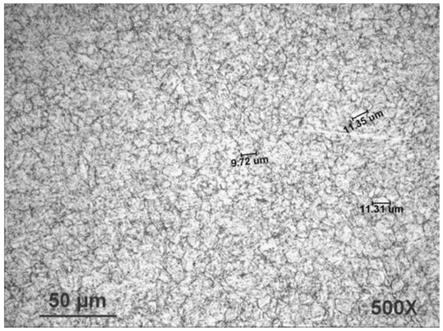
1.本發(fā)明屬于熱處理方法領(lǐng)域,具體涉及一種鋁型材擠壓模具鋼熱處理工藝。
背景技術(shù):
2.鋁型材是一種在高溫高壓下擠壓成型的通用型材,因此用于制造鋁型材的擠壓模具必須能夠承受較高的工作溫度和工作壓力。常規(guī)的鋁型材擠壓成型過程如圖1所示,鋁擠壓型材的生產(chǎn)是在擠壓機的作用下,通過擠壓桿100向鋁棒101傳遞壓力,鋁棒被強制壓入鋁擠壓模具102的模腔,強迫鋁金屬在模腔內(nèi)流動,最終在其模孔的工作帶103流出成型,得到型材104;鋁擠壓模具服役的條件非常惡劣,要求模具有很高的強度來承受擠壓應(yīng)力,尤其是其模孔的工作帶,不僅承受巨大的多向擠壓應(yīng)力,還承受著巨大摩擦應(yīng)力,工作帶還需具備很強的耐磨損能力,為了滿足鋁型材擠壓模具苛刻的服役條件,通常采用4cr5mosiv1熱作模具鋼制作。
3.4cr5mosiv1鋼(h13鋼)是所有熱作模具鋼中使用最廣泛的鋼號之一。該鋼具有較高的熱強度和硬度在中溫條件下具有很好的韌性熱疲勞性能和一定的耐磨性,由于鋼材的強韌性不夠,通常會造成型腔邊緣或局部塌陷、斷裂而早期失效。同時,由于在工作時與高溫熔融金屬相接觸,模具在冷卻過程中受到急冷急熱的熱沖擊,模具溫差較大,也容易導(dǎo)致熱疲勞失效。為適應(yīng)熱作模具惡劣的工作環(huán)境,防止模具在使用中產(chǎn)生早期斷裂及熱疲勞,通常要求熱處理后的模具應(yīng)當(dāng)有高的高溫硬度、高溫耐磨性、耐沖擊性能、斷裂韌性及回火穩(wěn)定性,因此,回火工藝對模具性能的提高起著至關(guān)重要的作用。
4.模具鋼常規(guī)熱處理工藝:淬火工藝溫度為1040℃,快速冷卻;后續(xù)進行兩次高溫回火,高溫回火溫度為580℃。常規(guī)熱處理工藝各工藝階段金相組織結(jié)構(gòu)分析結(jié)果如下:模具鋼在1040℃奧氏體化保溫結(jié)束時,此時金相組織結(jié)構(gòu)為奧氏體和少量未溶解到奧氏體中的碳化物;此時對模具鋼進行快速冷卻,在溫度接近馬氏體轉(zhuǎn)化點ms(~335℃)時,奧氏體開始向馬氏體轉(zhuǎn)化,連續(xù)冷卻至室溫,此時溫度離馬氏體轉(zhuǎn)變終了點mf(~-65℃)相差約100℃,因此還存在部分尚未轉(zhuǎn)化的奧氏體,稱為殘余奧氏體。
5.殘余奧氏體的形成原因有以下兩個方面:1、馬氏體的轉(zhuǎn)變是在一定溫度范圍內(nèi)進行,即在馬氏體開始轉(zhuǎn)變點ms至馬氏體轉(zhuǎn)變終了點mf之間進行,在連續(xù)冷卻過程中出現(xiàn)溫度停頓和降溫速度減慢,都會增大奧氏體的穩(wěn)定性和殘余奧氏體的量;2、奧氏體轉(zhuǎn)變成馬氏體過程中,會發(fā)生晶格改組,奧氏體屬于面心立方晶格系,馬氏體屬于體心立方晶格系,面心立方晶格的原子結(jié)構(gòu)排列比體心立方晶格的原子結(jié)構(gòu)排列更致密,即面心立方晶格系的奧氏體的比容小于體心立方晶格系的馬氏體,在奧氏體向馬氏體轉(zhuǎn)變過程中,材料體積發(fā)生膨脹,對尚未轉(zhuǎn)變的奧氏體構(gòu)成很大的壓應(yīng)力,導(dǎo)致奧氏體轉(zhuǎn)變空間被壓縮,失去轉(zhuǎn)變的條件,也會使得奧氏體向馬氏體轉(zhuǎn)變不能進行徹底。
6.因此,4cr5mosiv1模具鋼在1040℃奧氏體化后,快速冷卻到室溫時,其金相組織結(jié)構(gòu)為馬氏體、殘余奧氏體和少量的未溶碳化物;580℃第一次高溫回火時,過飽和的碳原子從馬氏體中析出,與合金元素結(jié)合形成碳化物,使得馬氏體的晶格畸變減少,空間被釋放;
在隨后冷卻到室溫的過程中,溫度接近馬氏體轉(zhuǎn)變ms點(335℃)時,殘余奧氏體開始向馬氏體轉(zhuǎn)變,一直冷卻至室溫,部分殘余奧氏體轉(zhuǎn)變成馬氏體,其金相組織結(jié)構(gòu)為高溫回火馬氏體、馬氏體和殘余奧氏體;580℃第二次高溫回火時,將第一次回火冷卻過程中形成的馬氏體中的碳原子析出,又釋放了小部分空間,在隨后的冷卻到室溫的過程中,又有極小量殘余奧氏體轉(zhuǎn)變成馬氏體,其金相組織結(jié)構(gòu)為高溫回火馬氏體、殘余奧氏體和極少量馬氏體,殘余奧氏體的硬度很低,耐磨性很差,常規(guī)熱處理工藝最終金相組織結(jié)構(gòu)示意圖如圖2所示,其中極少量的馬氏體200和殘余奧氏體202分布于高溫回火馬氏體i 201基體周圍。
7.模具鋼常規(guī)熱處理工藝完成,可投入使用,模具的模孔工作帶服役一段時間后,會出現(xiàn)磨粒磨損、粘著磨損和疲勞磨損,從而導(dǎo)致模孔變大,造成擠壓鋁型材的尺寸超出公差范圍,模具失效,報廢處理,因此模具的模孔工作帶過早磨損是制約著提高擠壓鋁型材生產(chǎn)效率的瓶頸,先進的熱處理工藝方法可以改變其內(nèi)部的金相組織結(jié)構(gòu),是提高模孔工作帶耐磨損性的途徑之一,因此需要探索發(fā)現(xiàn)新的熱處理工藝方法,改變其模孔的工作帶的內(nèi)部金相組織結(jié)構(gòu),提高模孔工作帶的耐磨損性,來延長模具的使用壽命,提高擠壓鋁型材的生產(chǎn)效率。
技術(shù)實現(xiàn)要素:
8.本發(fā)明要解決的技術(shù)問題是,提供一種延長鋁型材擠壓模具鋼的使用壽命的熱處理工藝。
9.為此,本發(fā)明提出一種鋁型材擠壓模具鋼的熱處理工藝,能夠提高模孔工作帶的耐磨損性。
10.本發(fā)明最關(guān)鍵的構(gòu)思在于:采用淬火、高溫回火、深冷處理和低溫回火來控制模具最終金相組織結(jié)構(gòu)。
11.模具鋼在各階段金相組織結(jié)構(gòu)為:模具鋼在淬火奧氏體保溫結(jié)束后,此時金相結(jié)構(gòu)為奧氏體和少量未溶解到奧氏體中的碳化物,對模具鋼進行快速冷卻至室溫,金相結(jié)構(gòu)轉(zhuǎn)化為馬氏體、殘余奧氏體和少量未溶碳化物;高溫回火時,過飽和的碳原子從馬氏體中析出,馬氏體的晶格畸變減少,空間被釋放,在隨后的冷卻到室溫的過程中,溫度接近為馬氏體轉(zhuǎn)變點ms(335℃)時,殘余奧氏體開始向馬氏體轉(zhuǎn)變,一直冷卻至室溫,部分殘余奧氏體轉(zhuǎn)變成馬氏體,其金相組織結(jié)構(gòu)為高溫回火馬氏體、馬氏體和殘余奧氏體;深冷處理時,模具鋼溫度保持在低于馬氏體轉(zhuǎn)變終了點mf(~-65℃)以下,奧氏體向馬氏體的轉(zhuǎn)變能增大,殘余奧氏體轉(zhuǎn)變成馬氏體,殘余奧氏體接近為零,其金相組織結(jié)構(gòu)為高溫回火馬氏體和馬氏體;低溫回火后,其金相組織結(jié)構(gòu)為高溫回火馬氏體和低溫回火馬氏體,低溫回火馬氏體的硬度比高溫回火馬氏體硬度要高,耐磨性好;最終實現(xiàn)模具鋼金相組織結(jié)構(gòu)為低溫回火馬氏體彌散分布于高溫回火馬氏體基體周圍。
12.位錯運動切行繞過低溫回火馬氏體如圖4所示,模具原子排列結(jié)構(gòu)存在不整齊的情況,出現(xiàn)錯位排列,稱為位錯,直線和彎曲箭頭代表位錯的運動方向,位錯運動時需要繞過低溫回火馬氏體ii 400。
13.根據(jù)本發(fā)明的實施方式的一種鋁型材擠壓模具鋼的熱處理工藝,包括以下步驟:
14.s1:淬火:將模具鋼控制溫度1050~1060℃保溫,保溫結(jié)束后冷卻至室溫;
15.s2:高溫回火:將步驟s1處理后模具鋼控制溫度580~590℃保溫,保溫結(jié)束后冷卻
至室溫;
16.s3:深冷處理:將步驟s2處理后模具鋼控制溫度零下135~零下125℃保溫,保溫結(jié)束后空熱至室溫;
17.s4:低溫回火:將步驟s3處理后控制溫度130~150℃保溫,保溫結(jié)束后冷卻至室溫。
18.熱處理過程中時,在模具鋼透熱的情況下,其保溫時間對性能影響很小,熱處理溫度對性能影響大,淬火加熱溫度越高,其晶粒越粗大,對力學(xué)性能影響越大,尤其會使模具鋼韌性降低。
19.根據(jù)本發(fā)明的一些實施方式,步驟s1所述保溫時間為180~240min。
20.保溫時間t=akd,其中t為加熱時間;a為加熱系數(shù)(單位:分鐘/毫米);d為擠壓模具有效厚度(單位:毫米);k為裝爐修正系數(shù),擠壓模具取2.0;該公式是淬火的保溫時間的計算方法,后續(xù)高溫回火的保溫時間是淬火保溫時間的1.5倍,低溫回火時間是淬火保溫時間的2倍,深冷處理的保溫時間是淬火保溫時間的3倍。根據(jù)本發(fā)明的一些實施方式,步驟s1所述冷卻方式為油冷。
21.根據(jù)本發(fā)明的一些實施方式,所述油冷介質(zhì)為真空淬火油,介質(zhì)溫度為60~80℃。
22.淬火冷卻方式對模具鋼的力學(xué)性能影響很大,水冷卻速度最快,但是組織結(jié)構(gòu)轉(zhuǎn)變應(yīng)力和冷熱應(yīng)力太大,兩者疊加在一起超過模具鋼強度會導(dǎo)致模具開裂;風(fēng)冷的冷卻速度太慢,溶解在奧氏體中的碳原子結(jié)合成碳化物從晶界上析出,弱化晶界,力學(xué)性能降低;一般采用油冷,冷卻速度溫和,滿足4cr5mosiv1熱作鋼cct曲線的要求。
23.根據(jù)本發(fā)明的一些實施方式,步驟s2所述保溫時間為270~360min。
24.根據(jù)本發(fā)明的一些實施方式,步驟s2所述冷卻方式為空冷。
25.根據(jù)本發(fā)明的一些實施方式,所述空冷為空氣中自然冷卻。
26.根據(jù)本發(fā)明的一些實施方式,步驟s3所述保溫時間為540~720min。
27.根據(jù)本發(fā)明的一些實施方式,步驟s3的空熱方式為空氣中自然回溫。
28.根據(jù)本發(fā)明的一些實施方式,步驟s4所述保溫時間為360~480min。
29.根據(jù)本發(fā)明的一些實施方式,步驟s4所述冷卻方式為空冷。
30.根據(jù)本發(fā)明的一些實施方式,所述室溫為20~30℃。
31.根據(jù)本發(fā)明的一些實施方式,所述模具鋼為4cr5mosiv1模具鋼。
32.根據(jù)本發(fā)明實施方式的一種鋁型材擠壓模具的熱處理工藝,至少具有如下有益效果:模具鋼在高溫回火后,部分殘余奧氏體轉(zhuǎn)變?yōu)轳R氏體,再經(jīng)過深冷處理后,剩余的殘余奧氏體轉(zhuǎn)變?yōu)槲诲e密度更高、較硬、更穩(wěn)定、耐磨性和耐熱性更高的馬氏體,再經(jīng)過低溫回火后,將深冷處理轉(zhuǎn)變得到的馬氏體,轉(zhuǎn)變?yōu)榈蜏鼗鼗瘃R氏體,并且呈彌散狀態(tài)分布在高溫回火馬氏體的基體上,在擠壓應(yīng)力作用下,微觀上位錯運動要切行或繞過這些低溫回火馬氏體,需要消耗更多的能量,宏觀上模具鋼展現(xiàn)強度更高,耐磨能力更強。
33.本發(fā)明工藝過程包括淬火、高溫回火、深冷處理、低溫回火四個步驟,改變了模具內(nèi)部金相組織結(jié)構(gòu),讓淬火后的殘余奧氏體轉(zhuǎn)變成低溫回火馬氏體,且彌散狀態(tài)分布在高溫回火馬氏體的基體上,從而改變模具鋼力學(xué)性能,模具鋼的室溫抗拉強度相比常規(guī)熱處理工藝高200mpa,達到2000mpa,同時模具鋼耐磨性顯著提高,依據(jù)實施例數(shù)據(jù)表明,一套擠壓直徑30的毫米實心鋁型材模具,可擠壓鋁型材60噸(現(xiàn)有水平為40噸),相比生產(chǎn)效率提
高三分之一,降低鋁型材的生產(chǎn)成本和縮短鋁型材的交貨周期。
附圖說明
34.圖1為鋁型材擠壓成型示意圖;
35.圖2為常規(guī)熱處理工藝最終金相組織結(jié)構(gòu)示意圖;
36.圖3為本申請熱處理工藝最終金相組織結(jié)構(gòu)示意圖;
37.圖4為位錯運動切行繞過低溫回火馬氏體示意圖;
38.圖5為實施例一金相圖譜;
39.圖6為實施例二金相圖譜;
40.圖7為對比例一金相圖譜;
41.圖8為對比例二金相圖譜;
42.圖9為對比例三金相圖譜;
43.圖10為對比例四金相圖譜;
44.圖11為對比例五金相圖譜。
45.標號說明:
46.擠壓桿100、鋁棒101、模具102、工作帶103、型材104、馬氏體200、高溫回火馬氏體i 201、殘余奧氏體202、高溫回火馬氏體ii 300、低溫回火馬氏體i 301、低溫回火馬氏體ii 400。
具體實施方式
47.為詳細說明本發(fā)明的技術(shù)內(nèi)容、所實現(xiàn)目的及效果,以下結(jié)合實施方式并配合附圖予以說明。實施例中所使用的試驗方法如無特殊說明,均為常規(guī)方法;所使用的材料、試劑等,如無特殊說明,均可從商業(yè)途徑得到的試劑和材料。本發(fā)明所稱i、ii并不代表需要同時出現(xiàn)或意味著先后順序,僅為便于區(qū)分。
48.本發(fā)明的實施例一為:一種鋁型材擠壓模具鋼的熱處理工藝,包括以下步驟:
49.s1:淬火:將模具鋼(4cr5mosiv1鋼)控制溫度為1050℃,保溫180分鐘,保溫結(jié)束后采用油冷至室溫;
50.s2:高溫回火:將步驟s1所得模具鋼控制溫度為580℃,保溫270分鐘,保溫結(jié)束后空冷至室溫;
51.s3:深冷處理:將步驟s2所得模具鋼控制溫度為零下125℃,保溫540分鐘,保溫結(jié)束后空熱至室溫;
52.s4:低溫回火:將步驟s3所得模具鋼控制溫度為130℃,保溫360分鐘,保溫結(jié)束后空冷至室溫。
53.本發(fā)明的實施例二:一種鋁型材擠壓模具鋼的熱處理工藝,包括以下步驟:
54.s1:淬火:將模具鋼(4cr5mosiv1鋼)控制溫度為1060℃,保溫180分鐘,保溫結(jié)束后采用油冷至室溫;
55.s2:高溫回火:將步驟s1所得模具鋼控制溫度為590℃,保溫270分鐘,保溫結(jié)束后風(fēng)冷至室溫;
56.s3:深冷處理:將步驟s2所得模具鋼控制溫度為零下135℃,保溫540分鐘,保溫結(jié)
束后空熱至室溫;
57.s4:低溫回火:將步驟s3所得模具鋼控制溫度為150℃,保溫360分鐘,保溫結(jié)束后空冷至室溫。
58.經(jīng)實施例一~二熱處理工藝制得的最終金相組織的結(jié)構(gòu)示意圖如圖3所示,包括高溫回火馬氏體ii 300和低溫回火馬氏體i 301,其中,低溫回火馬氏體i 301彌散分布于高溫回火馬氏體ii 300基體周圍。
59.本發(fā)明的對比例一為:一種鋁型材擠壓模具鋼的熱處理工藝,包括以下步驟:
60.s1:淬火:將模具鋼(4cr5mosiv1鋼)控制溫度為1050℃,保溫180分鐘,保溫結(jié)束后采用油冷至室溫;
61.s2:高溫回火:將步驟s1所得模具鋼控制溫度為580℃,保溫270分鐘,保溫結(jié)束后空冷至室溫;
62.s3:深冷處理:將步驟s2所得模具鋼控制溫度為零下100℃,保溫540分鐘,保溫結(jié)束后空熱至室溫;
63.s4:低溫回火:將步驟s3所得模具鋼控制溫度為130℃,保溫360分鐘,保溫結(jié)束后空冷至室溫。
64.本發(fā)明的對比例二為:一種鋁型材擠壓模具鋼的熱處理工藝方法,包括以下步驟:
65.s1:淬火:將模具鋼(4cr5mosiv1鋼)控制溫度為1050℃,保溫180分鐘,保溫結(jié)束后采用油冷至室溫;
66.s2:高溫回火:將步驟s1所得模具鋼控制溫度為580℃,保溫270分鐘,保溫結(jié)束后空冷至室溫;
67.s3:深冷處理:將步驟s2所得模具鋼控制溫度為零下100℃,保溫540分鐘,保溫結(jié)束后空熱至室溫;
68.s4:低溫回火:將步驟s3所得模具鋼控制溫度為180℃,保溫360分鐘,保溫結(jié)束后空冷至室溫。
69.本發(fā)明的對比例三為:一種鋁型材擠壓模具鋼的熱處理工藝,包括以下步驟:
70.s1:淬火:將模具鋼(4cr5mosiv1鋼)控制溫度為1040℃,保溫180分鐘,保溫結(jié)束后采用油冷至室溫;
71.s2:高溫回火:將步驟s1所得模具鋼控制溫度為580℃,保溫270分鐘,保溫結(jié)束后空冷至室溫;
72.s3:深冷處理:將步驟s2所得模具鋼控制溫度為零下125℃,保溫540分鐘,保溫結(jié)束后空熱至室溫;
73.s4:低溫回火:將步驟s3所得模具鋼控制溫度為130℃,保溫360分鐘,保溫結(jié)束后空冷至室溫。
74.本發(fā)明的對比例四為:一種鋁型材擠壓模具鋼的熱處理工藝,包括以下步驟:
75.s1:淬火:將模具鋼(4cr5mosiv1鋼)控制溫度為1080℃,保溫180分鐘,保溫結(jié)束后采用油冷至室溫;
76.s2:高溫回火:將步驟s1所得模具鋼控制溫度為600℃,保溫270分鐘,保溫結(jié)束后風(fēng)冷至室溫;
77.s3:深冷處理:將步驟s2所得模具鋼控制溫度為零下125℃,保溫540分鐘,保溫結(jié)
束后空熱至室溫;
78.s4:低溫回火:將步驟s3所得模具鋼控制溫度為100℃,保溫360分鐘,保溫結(jié)束后空冷至室溫。
79.本發(fā)明的對比例五為:一種鋁型材擠壓模具鋼的熱處理工藝方法,包括以下步驟:
80.s1:淬火:將模具鋼(4cr5mosiv1鋼)控制溫度為1050℃,保溫180分鐘,保溫結(jié)束后采用油冷至室溫;
81.s2:深冷處理:將步驟s2所得模具鋼控制溫度為零下125℃,保溫540分鐘,保溫結(jié)束后空熱至室溫;
82.s3:高溫回火:將步驟s1所得模具鋼控制溫度為580℃,保溫270分鐘,保溫結(jié)束后空冷至室溫;
83.s4:低溫回火:將步驟s3所得模具鋼控制溫度為130℃,保溫360分鐘,保溫結(jié)束后空冷至室溫。
84.實施例一~二和對比例一~五各性能測試方法如下:
85.1、抗拉強度:按國標gb/t228-2010要求,同批次鋼材縱向取樣,試樣直徑10毫米,長度100毫米,按照實施例和對比例的熱處理工藝方法完成后,在100噸的拉伸試驗機進行拉伸實驗,得出來的數(shù)據(jù)。
86.2、耐磨性:按國標gb/t34501-2017要求,同批次鋼材縱向取樣,試樣長*寬*高為15毫米*15毫米*5毫米,并磅好試樣重量,按照實施例和對比例的熱處理工藝方法完成后,在自動金相磨拋機上磨削5小時,取下試樣,再次磅試樣的重量,兩次重量差除以磨削前重量,得出的商,即為耐磨性,商的表示符號為g,g值越小,耐磨性越好。
87.3、金相圖譜:按adca北美壓鑄協(xié)會技術(shù)標準要求,同批次鋼材橫向取樣,試樣長*寬*高為15毫米*15毫米*10毫米,按照實施例和對比例的熱處理工藝方法完成后,試樣經(jīng)過磨拋百分之四的硝酸酒精溶液腐蝕后,在金相顯微鏡放大500倍,觀察到對比例和實施例最終熱處理組織結(jié)構(gòu)圖譜。
88.4、可擠壓型材:采用同批次鋼材,制造成同款鋁型材擠壓模具,按照實施例和對比例的熱處理工藝方法完成后,在擠壓機實際擠壓出的鋁型材的噸數(shù)。
89.實施例一~二與對比例一~五性能結(jié)果對比見表1。
90.表1實施例一~二與對比例一~五性能對比結(jié)果
[0091][0092][0093]
實施例一金相圖譜如圖5所示,從圖5可得出實施例一制得模具鋼金相圖譜結(jié)構(gòu)為高溫回火馬氏體和低溫回火馬氏體,低溫回火馬氏體彌散分布在高溫回火馬氏體的基體上,模具的強度硬度達到了最佳配合,在擠壓壓應(yīng)力的作用下,模具內(nèi)的位錯運動要切行和繞過這些彌散的低溫回火馬氏體,要消耗更大的能量,模具展現(xiàn)出優(yōu)良耐磨性,一套模具可以擠壓60噸鋁型材。
[0094]
實施例二金相圖譜如圖6所示,從圖6可得出實施例二組織結(jié)構(gòu)為高溫回火馬氏體
和低溫回火馬氏體,回火溫度對耐磨性有影響,回火溫度越高,模具的強度硬度降低,耐磨性也降低,590℃高溫回火的模具強度硬度要比580℃高溫回火的強度硬度要低些,因此一套模具擠壓鋁型材的產(chǎn)量與實施例1對比少2噸。
[0095]
對比例一金相圖譜如圖7所示,從圖7可得出對比例一組織結(jié)構(gòu)為高溫回火馬氏體、低溫回火馬氏體和極少量的殘余奧氏體,主要是由于深冷處理溫度采用零下100℃,深冷溫度高,殘余奧氏體完全轉(zhuǎn)變?yōu)轳R氏體的動能不足,還有有極少量的殘余奧氏體未完全轉(zhuǎn)變成馬氏體,殘余奧氏體的強度硬度比較低,耐磨性也相對差些,因此一套模具擠壓鋁型材的產(chǎn)量與實施例一對比要少4噸。
[0096]
對比例二金相圖譜如圖8所示,從圖8可得出對比例二組織結(jié)構(gòu)為高溫回火馬氏體、低溫回火馬氏體和極少量的殘余奧氏體,主要是由于深冷處理溫度采用零下100℃,深冷溫度高,殘余奧氏體完全轉(zhuǎn)變?yōu)轳R氏體的動能不足,還有有極少量的殘余奧氏體未完全轉(zhuǎn)變成馬氏體,殘余奧氏體的強度硬度比較低,加上低溫回火溫度采用的是180℃,雙重影響下,因此一套模具擠壓鋁型材的產(chǎn)量與實施例對比少6噸。
[0097]
對比例三金相圖譜如圖9所示,從圖9可得出對比例三組織結(jié)構(gòu)為高溫回火馬氏體和低溫回火馬氏體,模具淬火溫度采用1040℃,相比淬火溫度采用1050℃的,殘余奧氏體的量相對要少些,導(dǎo)致低溫回火馬氏體的量也少些,彌散分布的低溫回火馬氏體的量要少些,所以耐磨性相比淬火溫度采用1050℃~1060℃要些差些,因此一套模具擠壓鋁型材的產(chǎn)量與實施例對比少8噸。
[0098]
對比例四金相圖譜如圖10所示,從圖10可得出對比例四組織結(jié)構(gòu)為高溫回火馬氏體和低溫回火馬氏體,由于淬火溫度高,雖然殘余奧氏體的量多,彌散分布的低溫回火馬氏體的量也多,g值低耐磨性好,但是奧氏體晶粒粗大,其晶粒直徑平均有21.5微米,韌性降低,斷裂前吸收能量的能力降低,模具在使用中出現(xiàn)脆性斷裂,因此一套模具擠壓鋁型材的產(chǎn)量與常規(guī)熱處理少10噸,與實施例1對比少30噸。
[0099]
對比例五金相圖譜如圖11所示,從圖11可得出對比例五組織結(jié)構(gòu)為高溫回火馬氏體,為單相組織結(jié)構(gòu),淬火后進行深冷處理,再進行高溫回火,其金相組織轉(zhuǎn)變成單一的高溫回火馬氏體組織結(jié)構(gòu),與常規(guī)熱處理的組織結(jié)構(gòu)相比,只是沒有殘余奧氏體,耐磨性比常規(guī)熱處理稍好,因此一套模具比常規(guī)熱處理的模具可多擠壓2噸鋁型材,但是相比對比例1要少擠壓18噸鋁型材。
[0100]
綜上所述,本發(fā)明提供的模具鋼熱處理工藝,改變了模具鋼內(nèi)部金相組織結(jié)構(gòu),使得模具鋼淬火后的殘余奧氏體轉(zhuǎn)變成低溫回火馬氏體,并且是彌散狀態(tài)分布在高溫回火馬氏體的基體周圍,達到了改變其力學(xué)性能的效果,模具鋼的室溫抗拉強度達到2000mpa,耐磨性顯著提高,生產(chǎn)數(shù)據(jù)表明,一套擠壓直徑30的毫米實心鋁型材模具,可擠壓鋁型材60噸,采用常規(guī)熱處理的模具鋼其產(chǎn)量僅為40噸,相比生產(chǎn)效率提高三分之一,降低了鋁型材的生產(chǎn)成本和縮短了鋁型材的生產(chǎn)周期,具有良好的工業(yè)應(yīng)用前景。
[0101]
以上所述僅為本發(fā)明的實施例,并非因此限制本發(fā)明的專利范圍,凡是利用本發(fā)明說明書及附圖內(nèi)容所作的等同變換,或直接或間接運用在相關(guān)的技術(shù)領(lǐng)域,均同理包括在本發(fā)明的專利保護范圍內(nèi)。
上一篇:沒有了
下一篇:一種Cr5系列熱作模具鋼的制作方法
下一篇:一種Cr5系列熱作模具鋼的制作方法